Episodes
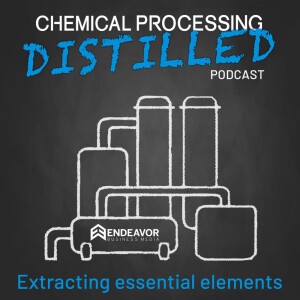
23 minutes ago
Outlook of the Chemical Industry: Confused Sea State
23 minutes ago
23 minutes ago
Get your sea legs ready. The economy is getting choppy, according to Martha Gilchrist Moore, chief economist and managing director, economics and statistics at the American Chemistry Council (ACC).
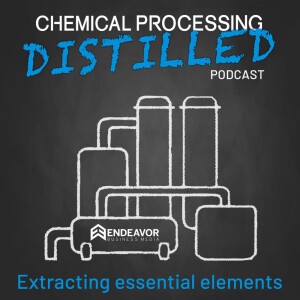
Friday Jul 04, 2025
Why Chemical Plants Are Burning Cash Instead of Recovering Heat
Friday Jul 04, 2025
Friday Jul 04, 2025
Are you leaving $7.7 million on the table? A single chemical plant identified annual energy savings worth that much through an analysis that took just months to complete. The payback period? Less than two years. The solution? None other than your chemical engineering 101 heat integration through pinch analysis and heat exchanger network optimization.
Editor-in-Chief Traci Purdum reads the latest Energy Saver column written by Thomas Kwan.
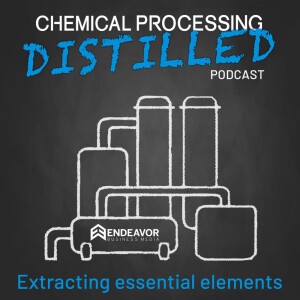
Friday Jun 27, 2025
Friday Jun 27, 2025
The Trump administration has proposed to eliminate the U.S. Chemical Safety and Hazard Investigation Board by October 2026, citing fiscal responsibility and redundancy. Industry experts oppose this move, warning it would remove crucial disaster prevention oversight despite the agency's modest $14 million budget. Meanwhile, recycling advances continue: Eastman expanded molecular recycling operations to 110,000 metric tons annually in Tennessee, while BASF launched Europe's largest battery recycling plant, processing nearly 40,000 EV batteries yearly. On the innovation front, Department of Energy researchers developed a photosynthesis-inspired catalyst that selectively converts CO2 into formate using light, potentially revolutionizing industrial chemical production by avoiding unwanted byproducts that plague current conversion methods.
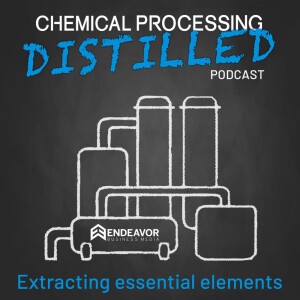
Monday Jun 23, 2025
Celebrating International Women In Engineering Day
Monday Jun 23, 2025
Monday Jun 23, 2025
Did you know that today — June 23 — is International Women in Engineering Day (INWED)? Launched by the Women’s Engineering Society (WES) in the UK in 2014, the event has since grown into an internationally recognized awareness campaign celebrated by various organizations, institutions, and individuals around the world. Each year, INWED adopts a specific theme to focus on women’s contributions to engineering and STEM. This year’s theme is “Together We Engineer.”
From the days of Cleopatra to contemporary chemical engineers, we look at the women who transformed modern life through innovations touching nearly every aspect of human existence.
#INWED2025
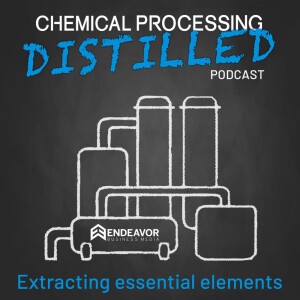
Friday Jun 20, 2025
Turn Training Hopes Into Measurable Success
Friday Jun 20, 2025
Friday Jun 20, 2025
In this episode, Traci and Dave focus on training evaluation as the final component of instructional system design. Dave explains that evaluation has two aspects: specific (assessing whether students learned what was taught in a particular course) and global (determining if training improves actual job performance).
The key insight is that evaluation methods should align directly with learning objectives. If objectives are correctly written to be objective and measurable, they define how students should be evaluated. Most companies fail at proper evaluation, relying on subjective assessments rather than objective testing.
High-fidelity simulators and process data can measure actual performance improvements in real-world transfer evaluations. However, evaluation should focus on system performance rather than individual blame.
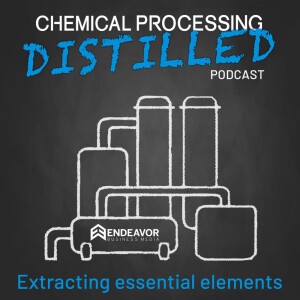
Friday Jun 13, 2025
Small Acts, Big Impact: How Micro-Behaviors Shape Teams
Friday Jun 13, 2025
Friday Jun 13, 2025
In Case You Missed It brings the written word to life. In today’s episode, Editor-in-Chief Traci Purdum will read an article from Lauren Neal, Chemical Processing’s Workforce Matters columnist. This column “Small Acts, Big Impact: How Micro-Behaviors Shape Teams” was published to our website June 4, 2025
You know that feeling. You’re in a team meeting, presenting a solid idea, and someone smirks. Another person rolls their eyes. Then silence.
No one says a word.
That’s a micro-behavior. A subtle action that doesn’t show up in the org chart or the risk register but does show up in the culture and your team’s morale, retention and performance.
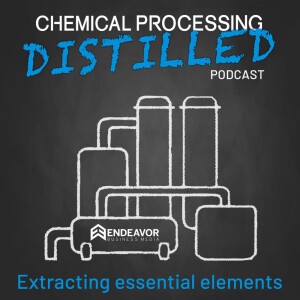
Friday Jun 06, 2025
Trump Cuts, EPA Restructures, ExxonMobil Expands
Friday Jun 06, 2025
Friday Jun 06, 2025
In this episode, Executive Editor Jonathan Katz reviews the top news stories for May 2025.
Trump's budget cuts and EPA changes reshape the chemical industry amid expansion.
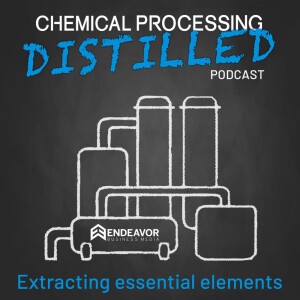
Friday May 23, 2025
Operator Training Inefficiency Costs Millions
Friday May 23, 2025
Friday May 23, 2025
In Chemical Processing's Distilled Podcast, we discuss flaws in operator training, focusing on "time to train." Companies can waste millions of dollars by not optimizing training duration, often using fixed-length programs regardless of trainees' prior experience. Feedback loops to adjust training time based on individual competency and learning objectives are imperative. Indeed, proper assessment could identify struggling trainees and high performers who could be fast-tracked.
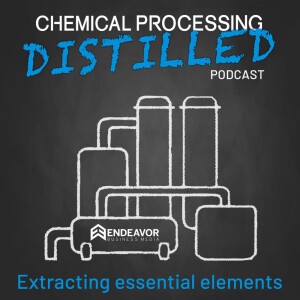
Friday May 16, 2025
9 Best Practices for Reliability and Maintenance
Friday May 16, 2025
Friday May 16, 2025
This episode from Chemical Processing's Distilled podcast shares industry best practices for chemical plant reliability and maintenance. Key recommendations include understanding equipment failure modes through predictive maintenance techniques like vibration analysis and thermography, developing balanced preventive maintenance programs that avoid over-maintaining equipment, and conducting thorough root cause analysis using methods such as 5-why analysis and fishbone diagrams.
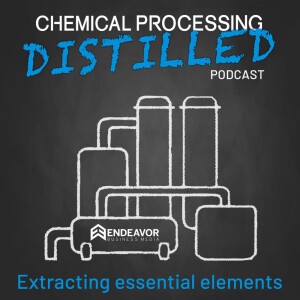
Friday May 09, 2025
Chocolate: From Theology and Processing to Functional Food
Friday May 09, 2025
Friday May 09, 2025
With Easter just behind us and chocolate consumption hitting its second-quarter 2025 peak, it’s a good time to reflect on the theological and processing developments that have got us where we are today.
In this In Case You Missed It Episode, Chemical Processing's Editor-in-Chief Traci Purdum brings the written word to life, and Seán Ottewell, editor-at-large, provides the story.
The original column was posted to the site on May 5, 2025.
Chocoholics unite!